Worn, grooved, or damaged brake discs will dramatically affect stopping distance and can also cause severe vibrations in the steering wheel when brakes are applied, causing loss of control under hard braking. For even the most novice mechanic, this is a simple DIY job that can be completed with common hand tools.

Materials Needed
- Low profile jack
- Jack stands
- 15 mm socket and ratchet (caliper bolts)
- 16/18 mm wrench (rear/front caliper bolt collar)
- 13/16" socket and 1/2" ratchet
- Loctite
- Hammer
- Screwdriver
- Brake cleaner
- Torque wrench
- C-clamp or caliper reset tool
Step 1 – Loosen lug nuts, jack vehicle and remove wheel
Using the jacking points in front of the rear wheels or behind the front wheels, raise the car enough to remove the wheel. Never jack the car using suspension components or any part of the body as this may cause damage. It is also recommended that you use either a small block of wood or jacking pucks. Once the car is raised properly, place jack stands under the vehicle.
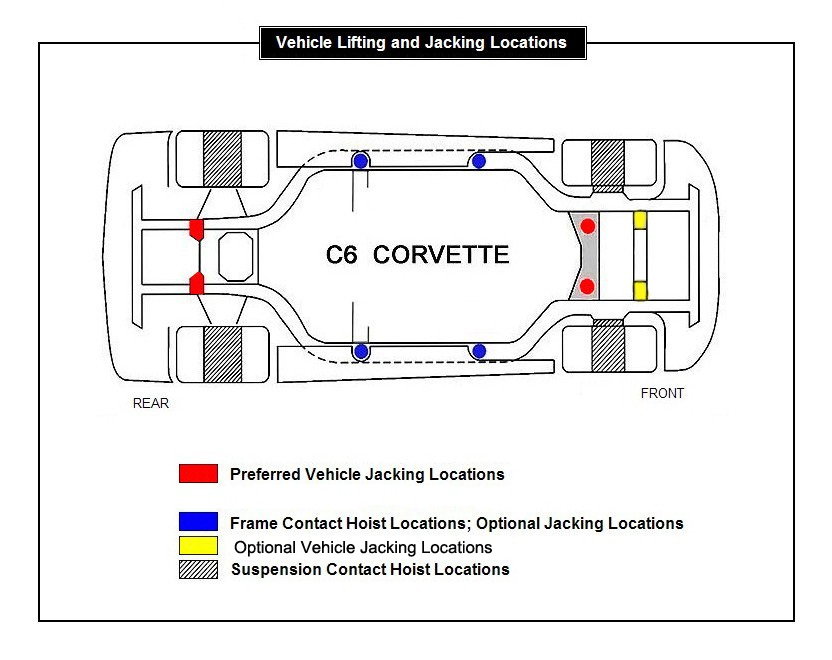
Step 2 – Check the fluid in the master cylinder
Caliper decompression is necessary and it will force brake fluid back into the master cylinder, so either remove some fluid (if necessary) or secure shop rags around the master cylinder for potential overflow. Leave the cover off the master cylinder, so that you will not be working against the pressure of a closed system.
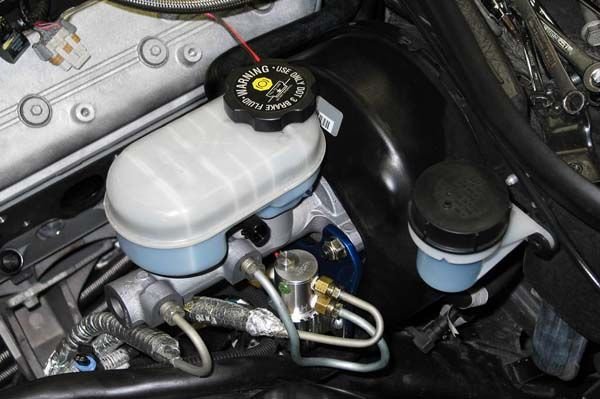
Step 3 – FRONT BRAKES Loosen the caliper bolts
The caliper is mounted to the carrier via two 22mm bolts on the backside of the hub. These are large bolts and on there quite tight (70 ft./lb.) so a larger ratchet, or breaker bar would be a good idea here. Remove these two bolts and you should be able to wiggle the caliper off the rotor. Mind your brake lines, and don't pull too hard! With the caliper free, there is nothing securing the rotor to the hub, so if it feels like it's going to slide off, just remove it and set it aside for now.
-
Figure 3. Location of caliper bolts on backside of hub. -
Figure 4. Wiggle caliper off rotor, mind your brake lines!
Step 4 – Compress the pistons
The standard C6 calipers utilize a two-piston design, with both pistons being on the hub-side of the caliper, as opposed to one piston on each side. This is a bit less efficient for extreme performance situation, but it is easy to service! The brake pads should now be free to be removed. Remove the outer pad, and leave the inside pad intact. As brake pads wear, the brake caliper pistons extend further out to keep pressure against the pads the rotors. New pads are much thicker, and will not all fit in the caliper along with the rotor without compressing those pistons. Use a C-clamp and press against the inside brake pad and the outside of the caliper. Exerting this pressure on the pad will compress the pistons simultaneously, as opposed to trying to compress one at a time, which could damage the calipers if done incorrectly. Tighten the clamp slowly until the two pistons are compressed just short of all the way in. Compressing the pistons will allow more room for the new, thick pads to fit around the rotor.
-
Figure 5. Remove the outer brake pad. -
Figure 6. Use a C-clamp against the inside pad to compress the caliper pistons.
Warning
Do not let the caliper hang and create tension on the brake line. This could damage the brake line and cause premature failure. Either secure the caliper using wire or rope to hang without tension, or rest it on a box/crate placed under the car.
Step 5 – Clean and apply lube
At this point, inspect all brake parts and use brake cleaner to clean the system of brake dust and debris. Before installing the new the pads, apply brake lube (dry film) to the the backing plate of the new pads.
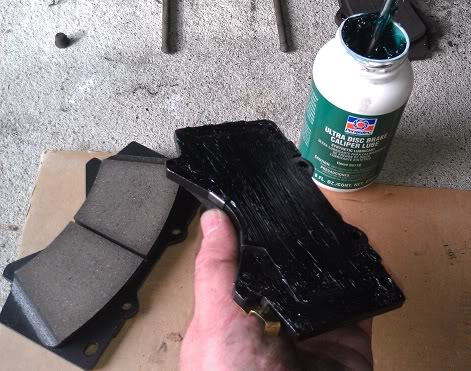
Warning
Do not allow lubricant to contact the rotor or face of the pads. This is important as friction creates stopping power and lubricant will decrease friction. Also, do not overdo it as excess lubricant may drip onto those parts.
Step 6 – Remove disc
If still present from the factory, remove the spring washers from the wheel studs using a flat screwdriver and discard as these will not have to be reused. At this point the disc should slide freely over the wheel studs; some light tapping on the rear with a hammer may be necessary.
-
Figure 3. Indication of a bad brake disc. -
Figure 4. Remove the disc.
Step 7 – Install new rotors
At this point, it's time to install the new brake rotor. Be sure to inspect the wheel bearing flange for rust or debris and, if necessary, clean. Slide the new disc over the wheel studs and clean any fingerprints or grease from the disc using brake cleaner. Next, re-install the caliper mounting bracket using Loctite and torque to 125 ft/lbs.
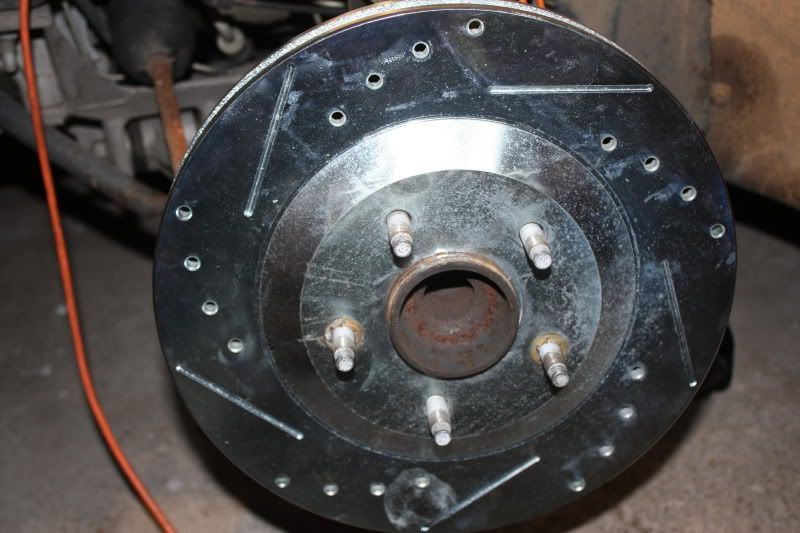
Step 8 – Install the new pads and place the caliper in place
Make sure that the friction side of the new pads faces the rotor, both inboard and outboard. Make sure to position the pad wear sensor, located on the inboard pad, so that it is in the trailing position as the brake pad wears and moves forward toward the rotor.
Slide the caliper, with pads around the rotor. If you didn't compress the pistons enough, this will prove difficult. If you need to further compress the pistons, utilize the same C-clamp method and then try again. With the caliper secured around the rotor, reconnect the two large caliper-carrier bolts to approximately 70 ft./lbs., or "pretty snug," and you should be done.
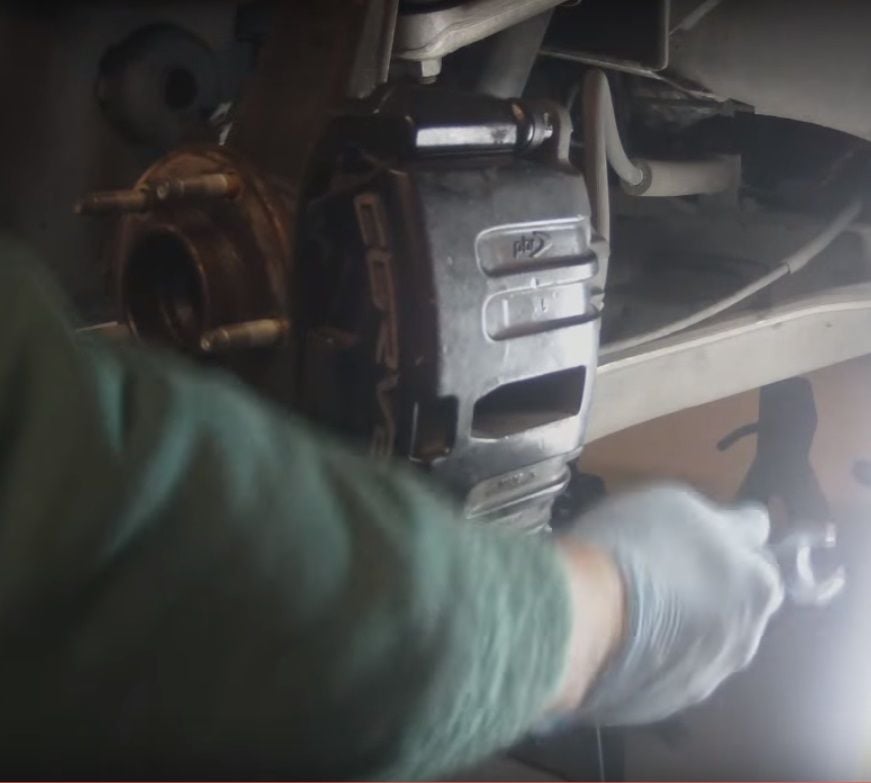
Step 9 – Repeat this procedure on the other side
Repeat the process for the other side completing axle set. Check the master cylinder as the fluid level may have changed. As brake pads wear, the brake fluid level may appear lower, as the caliper pistons are pushed further out. Fresh brake pads keep the pistons from traveling as far, which tends to push the brake fluid back into the reservoir, raising the level.
Step 10 – REAR BRAKES Loosen bolts and compress pistons
Using 15mm and 18mm wrenches or sockets, loosen the caliper guide pin bolts located on the inboard side of the caliper.
Since the caliper position adjusts as the pads wear, they will need to be decompressed to allow for the space necessary for the new thicker pad.
- To compress pistons before removing caliper, place a large C-clamp over the caliper body and center it, so that the force is evenly distributed. Use an old pad or wood block, so you don't damage the caliper and it will help distribute the force. Slowly tighten the clamp, so that the pistons are pressed back into the caliper bores. Once the pads are free from the rotor, completely remove the guide pin bolts and remove the caliper. You may find that you can remove the old pads without removing the caliper, but it is suggested removing the caliper to inspect all parts and prepare for proper re-installation.
- To decompress the pistons after removing the caliper, completely remove the guide pin bolts. Pivot the caliper to remove it from the rotor. Use a brake reset tool to decompress the caliper piston into the caliper bores. This tool is easy to use and is adjustable for all caliper/piston sizes and made so that you will not damage the caliper.

Pro Tips
- Do not let the caliper hang because it creates tension on the brake line. You can either secure the caliper using a wire or rope to hang without tension or rest it on a box/crate under the car.
- A brake reset tool is free to rent for a day at most major auto stores like Autozone.
Step 11 – Remove the caliper bolts and slide the caliper from the brake rotor
Using the 15 mm socket and either the 16 mm wrench (rear) or 18 mm wrench (front), remove the caliper bolts and slide the caliper off the brake disc. Support the brake caliper using a plastic zip tie or wire in between one of the holes, but do NOT let the caliper hang free using only the flexible rubber brake line. Once the caliper is removed, using the 13/16" socket, remove the caliper bracket bolts. These bolts have Loctite on them from the factory and may require some force and a breaker bar to remove.
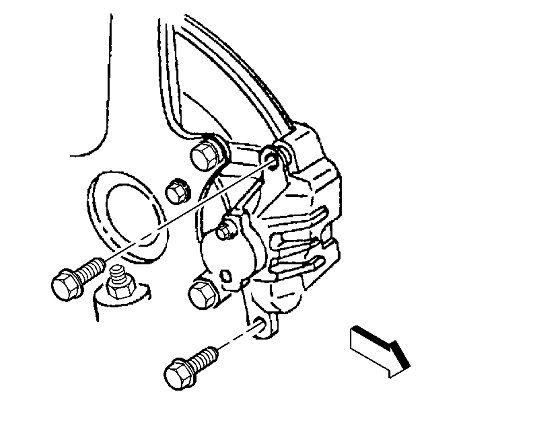
Step 12 – Remove the old pads
Remove spring or retainer and the old pads from the caliper by simply pulling them out. Make note of the location of the pads in regards to the retainer.
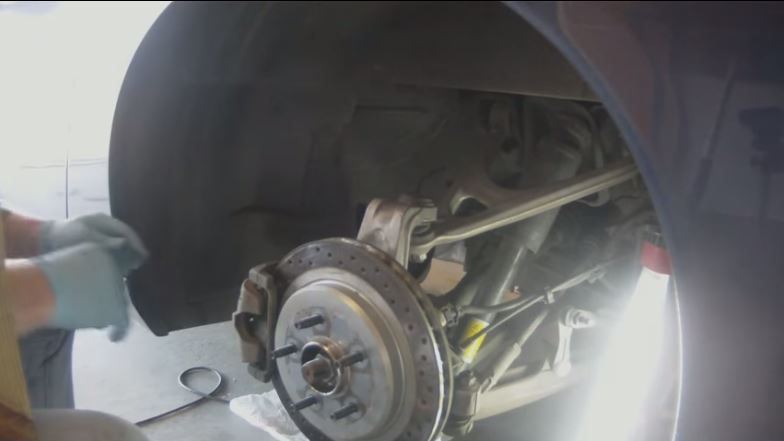
Pro Tip
Taking a picture with your cell phone is a great way to document components and their positions to insure proper re-installation.
Step 13 – Install the new pads and retainer
At this point, inspect all brake parts and use brake cleaner to clean the system of dust or debris. Before installing the new the pads, apply brake lube (dry film) to the the backing plate of the new pads.
Mount the new retainer and pads to the caliper. Make sure that the friction side of the new pads faces the rotor (both inboard and outboard). Make sure to position the pad wear sensor, located on the inboard pad, so that it is in the trailing position as the brake pad wears and moves forward toward the rotor.
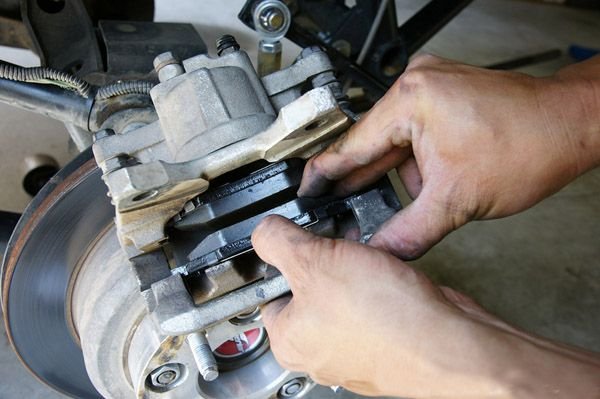
Pro Tip
Do not allow lubricant to contact the rotor or face of the pads. This is important as friction creates stopping power and lubricant will decrease friction. Also, do not overdo it as excess lubricant may drip onto those parts.
Step 14 – Remove disc
If still present from the factory, remove the spring washers from the wheel studs using a flat screwdriver and discard as these will not have to be reused. At this point the disc should slide freely over the wheel studs; some light tapping on the rear with a hammer may be necessary.
-
Figure 3. Indication of a bad brake disc. -
Figure 4. Remove the disc.
Step 15 – Install new discs and attach brake caliper bracket and caliper
At this point, it's time to install the new brake disc. Be sure to inspect the wheel bearing flange for rust or debris and, if necessary, clean. Slide the new disc over the wheel studs and clean any fingerprints or grease from the disc using brake cleaner. Next, re-install the caliper mounting bracket using Loctite and torque to 125 ft/lbs. Finally, position the caliper back into the caliper bracket ensuring that the brake pads have remained in place and that there aren't any fingerprints or grease on the face of the brake pads. Use Loctite on the caliper bolts as well and torque to 23 ft/lbs.
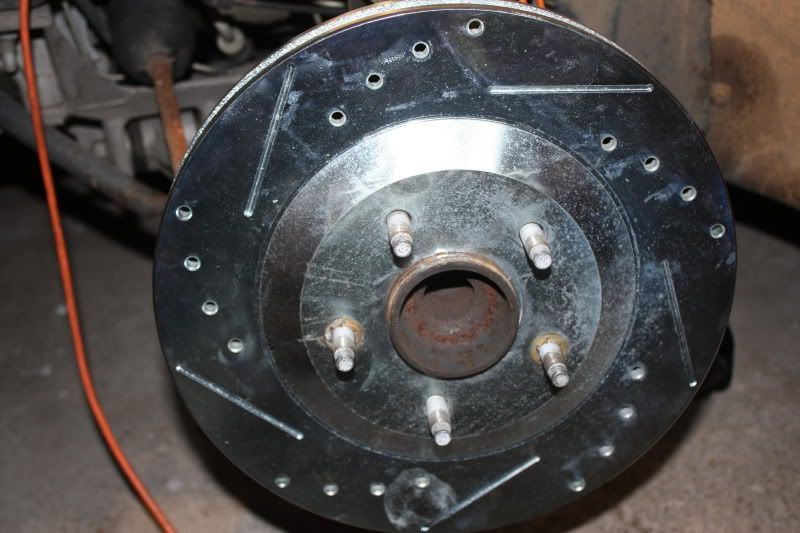
Step 16 – Install the caliper in place
Guide the caliper assembly over the rotor. At this point, you may find that you have to decompress the caliper piston further to allow for the thicker new pads. Do this using the C-clamp method (taking precaution not to damage the caliper) or use the reset tool. Attach the brake caliper guide pin bolts and tighten.
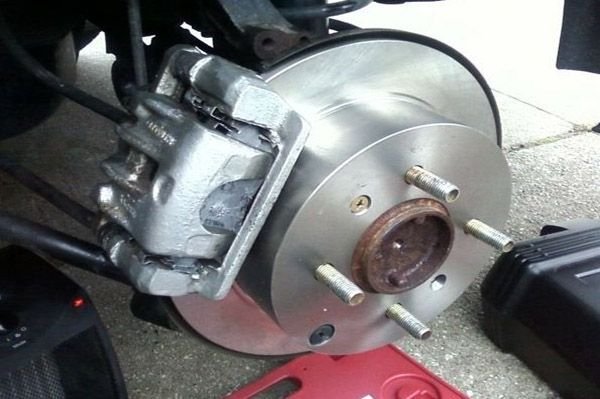
Step 17 – Re-install wheels and lower vehicle
Re-install the wheel and torque the lug nuts to 100 ft/lbs. Using the jack, raise the vehicle and remove the jack stands, then slowly lower the vehicle back down to the ground. Before driving the vehicle, it's a good idea to start the engine and pump the brake pedal a few times to re-seat the brake pads.
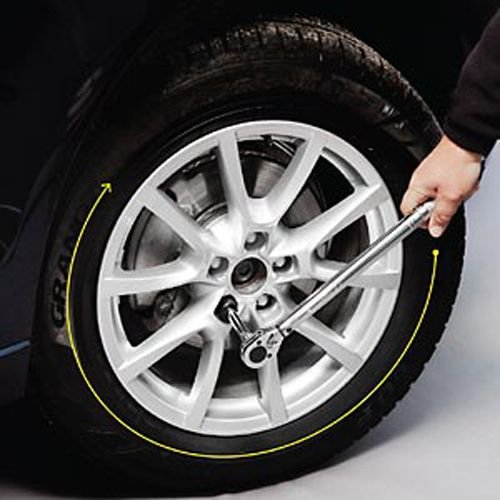